Deep-sea sediment sampler
Motivation
Our device, Archie, increases accessibility to hadal depth (10,000 m) sediment core samples, broadening our limited understanding of the deep sea. Currently, only a handful of vehicles are capable of traveling to the bottom of the Mariana Trench due to extreme temperatures and pressures as well as challenges with navigation. Inkfish Technology reached out to our lab with the hope that we could develop a deep-sea sediment sampler module compatible with their lander. These samples are crucial for assessing the health of the deep-sea environment and gaining insights into the organisms that currently or historically inhabited the seabed.
Project information
- CategoryResearch project
- Project dateFall 2023 - Present
- Skills usedCNC, milling, lathe, CAD
System Highlights
Archie is a novel device that utilizes the height differential between a sliding and fixed frame and steel cables to insert a collection tube in the ground. Once collection is complete, it uses compression springs to retract the collection tube back into the main assembly. A core catcher at the bottom of the collection tube and a valve at the top allow the sample to enter through the bottom and preserve the layers of sediment during the lander’s ascent and retrieval. Finally, the sampler is connected to the lander with drawer slides so that the bottom of the sampler moves below the bottom of the lander after the lander is deployed. This creates the height differential used for sample collection.
My contribution
TThe research project was comprised of four undergraduate researchers. The entire team was involved in the initial design stage brainstorming methods to utilize only mechanical energy storage to collect and retain soil sediment. I worked on the sliding frames which triggered the collection and retraction of the sampling tube.
Reflection
There were a lot of design, fabrication, and material considerations that went into developing a system that could survive the harsh conditions of the bottom of the ocean. For example, the compression due to pressure is not uniform for different materials so it was important to only utilize low-precision interfaces and maximize the number of parts that can be made from a singular material. It was also interesting to design an entirely mechanically actuated system; it was similar to creating a Rube Goldberg system (Fun fact: that’s where “Archie” got his name; it sounds like “R.G.”). I also gained a lot of machining experience during this project, especially with the CNC mill. Before, I had only used it a few times and had the theoretical knowledge to machine parts, but I wasn’t fully comfortable with the equipment. After spending many hours babysitting the Tormach Mill, I am more confident using and troubleshooting its issues. Archie is currently going on its first expedition in Tonga for a shallow water (3,000 m) validation, and I’m excited for the results of the test.
Design requirements
Our system must face several key constraints:
To solve these issues:
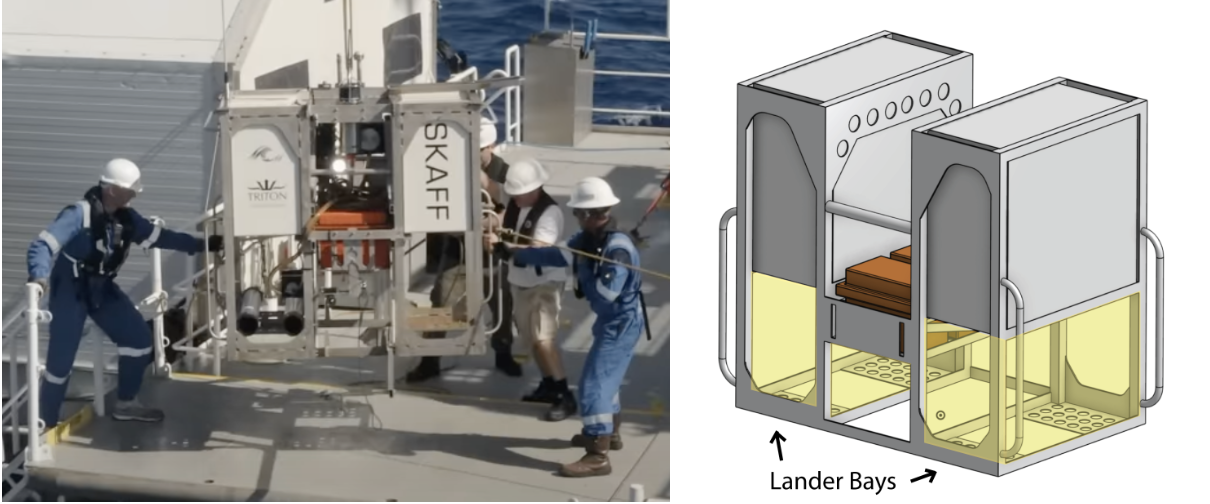
Overview
When the lander is initially deployed and descends, the sampler will sit below the bottom of the lander.
Once the lander nears the seafloor, there are three stages to the collection process:
- In the first stage, the base plate of the sampler lands and settles against the seafloor.
- In the second stage, the lander continues to sink until it makes contact with the seafloor. The weight of the lander and the force of the seafloor upwards act on the base plate to trigger a spring-pulley system that inserts the collection tube into the sediment.
- In the third and final stage, the tube is retracted from the sediment, and the base plate reaches its final position within the lander’s bay.
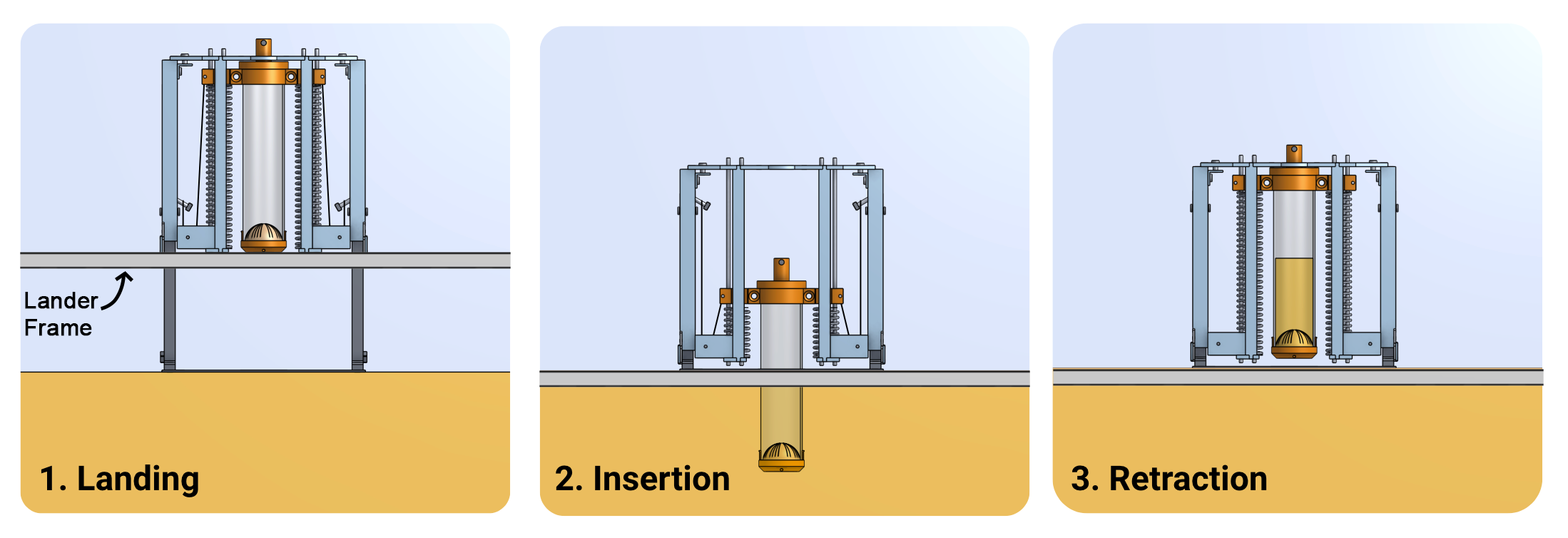
Once the collection tube has been retracted, the lander can begin its ascent with the sampler and sample safely tucked away into the bay.
Collection tube subsystem
The collection tube captures sediment once the lander reaches the seafloor and secures it until retrieval, minimizing disturbance to the top layers of the seafloor.
The subsystem consists of:
The ball valve uses a spring and o-ring to allow water to pass as the tube drives into the ground but creates a strong seal during ascension. In images 1 and 2, the tube is being driven into the ground, so water pushes the spring-ball upward, opening the seal. In image 3, as the lander ascends, water flows from above, pushing the ball into the o-ring to create a secure pressure seal.
The core catcher apparatus is a hollow demi sphere-shaped piece of plastic. The hollow demi-sphere shape is formed by a ring of slightly triangular-shaped fingers that are pushed open by entering sediment and closed upon retraction from the upward motion of the tube paired with the weight of the sediment. This design results in sediment layers mixing at the edges of the core sample, but sediment layers at the center of the sample will be preserved. We originally tried to make this shape with thinly cut sheet metal, but testing reveals that an off-the-shelf core-catcher was more effective.
Frame subsystem
The frame subsystem is responsible for driving and removing the collection tube into the seafloor. The system can be broken into two parts: the static system and the dynamic system.
The static system remains permanently fixed relative to the lander. The top plate, rod plate, aluminum rails, and box tube extrusions are the foundation of the static segment and provide the majority of the frame’s stiffness. The 6 aluminum rods prevent the spring from shifting or buckling during compression. There are also two pulleys connected to the static frame.
The dynamic subsystem slides relative to the lander, drives the tube into the soil, and once triggered, retracts the collection tube into the lander bay. The dynamic system is the core of the mechanical sediment collection and consists primarily of two Delrin posts fastened to a base plate. At the top of each post is a pocket for the tooling ball. There are four cables that attach to an arm on the tooling ball, go around the pulley, and connect to a rod at the side of the collection tube cap.
The core of the frame subsystem is a spring-pulley mechanism that utilizes the change in distance to push the collection tube into the sediment and eventually pull the collection tube out. While the lander is descending, the base plate sits below the bottom of the lander and will make contact with the ground first. The weight of the lander will push the Delrin posts into the box tubes. As the post travels up, the tension in the cables will drive the collection tube into the ground and compress the two springs. The post will slide up 159mm where the tooling balls are pulled out of the post, releasing the tension in the cable, allowing the springs to decompress and push the tube into the landing bay.
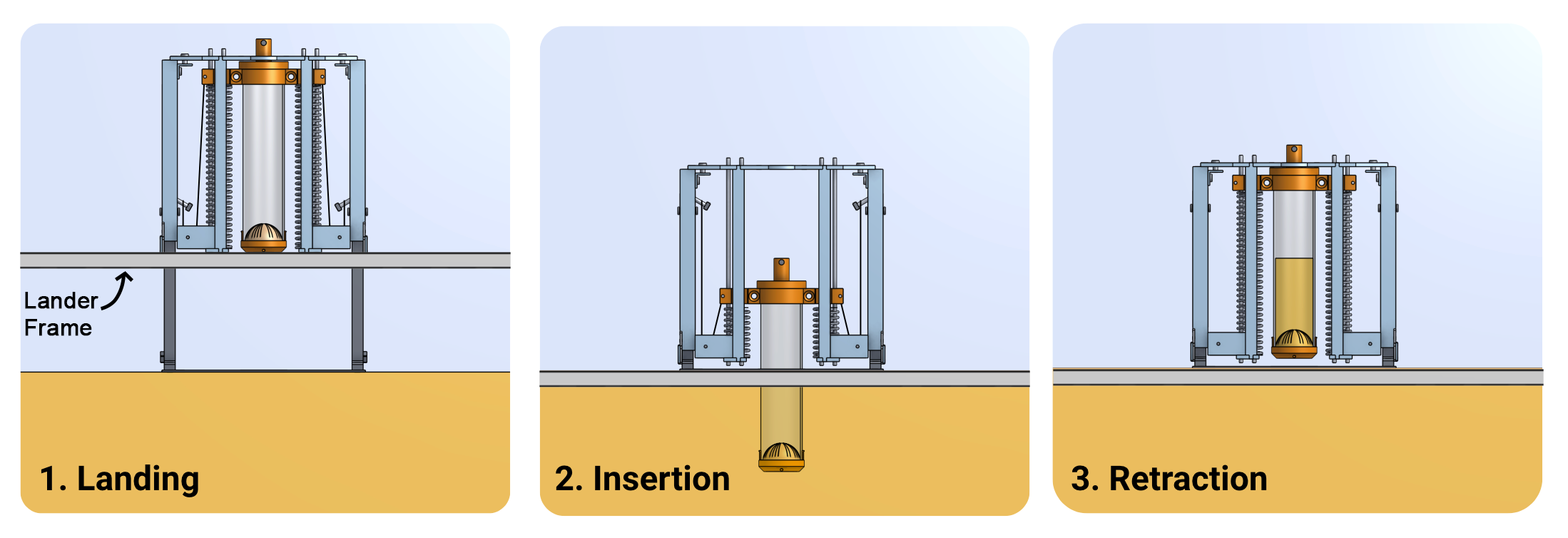