Kaplinko
About this project
MIT's 2.007 (Design and Manufacturing I) is a hands-on, project-based course where we design, build, and test robots and mechanical systems to compete in a robot competition at the end of the semester. We focus on applying mechanical engineering principles, using tools like CAD, machining, and electronics to create practical engineering designs.
Project information
- CategoryCourse project
- Project dateSpring 2022
- Skills usedMilling, lathe, CAD
The challenge
The game field included several tasks, of which I attempted four:
- Lifting the beaver to 12, 24, or 40 in
- Press buttons to release balls into the pachinko board
- Pull on a ring
- Tip the street lamp
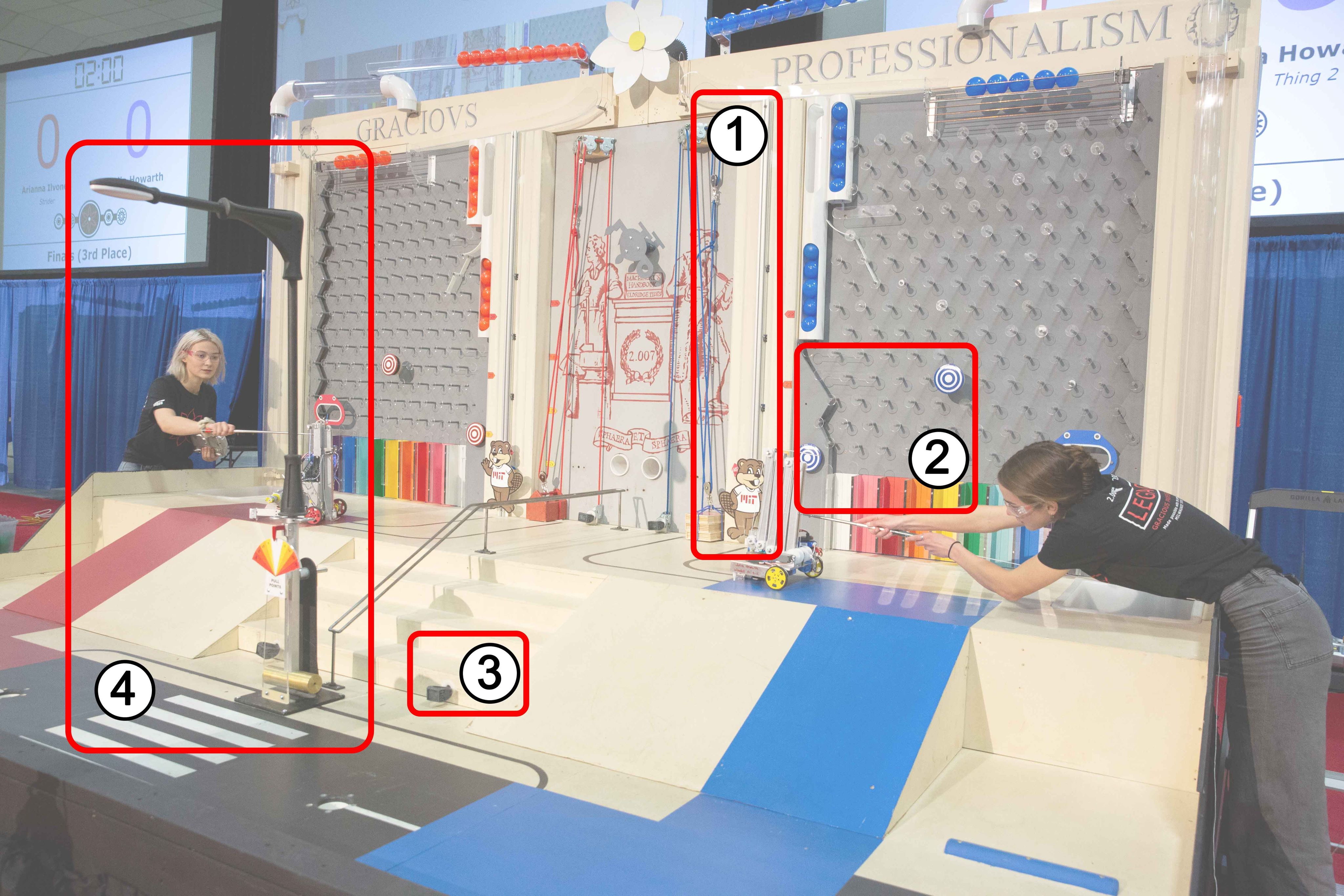
Meet my robot, Kaplinko!
My goals for my robot included:
To minimize overall robot dimension to meet starting size regulation, I designed mechanisms that can be used to score multiple tasks. Kaplinko is made of 3 main modules the chassis, the lift mechanism, and hook attachment.
Chassis
The chassis is a four-wheel belt tank drive to maximize traction. This was important in order to drive up and down the 25-degree slope and to pull on the ring. The system is powered by two motors which are on opposite sides to decrease the overall robot width. The chassis is made from laser-cut and bent sheet metal to increase precision and customization. The top of the chassis had a hole pattern to easily mount, test, and iterate on other modules.
Lift
The main goals for the lift mechanism were to raise the 5kg beaver up 40 inches, press the bullseye buttons, and tip the street car lamp. Some constraints imposed was the robot cannot exceed 16” in its starting position and access to limited motor selections.
The lift is made from aluminum box extrusions which are connected by a Delrin roller assembles that slide between adjacent extrusions. A string, controlled by a motor, transfers motion through tension and pulleys to raise or lower the lift. Attached to the end of the lift is a platform to push up the beaver and press buttons and sheet metal to pull and tip the street lamp. Force and motor calculations were used to determine the optimal size of the spool the string wraps around to lift the beaver as quickly as possible.
Hook
The hook is a laser-cut aluminum piece controlled by a servo. It secures the robot to the ring before driving forward, pulling the ring out.